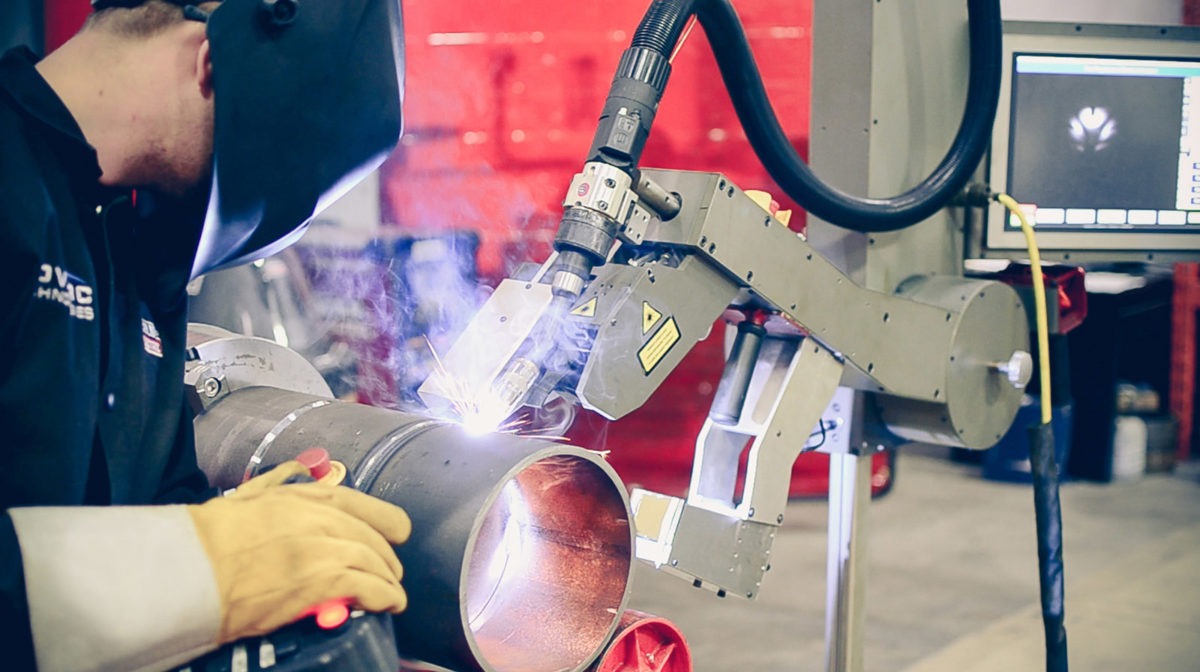
Welding Automation
Welding automation uses robots to increase the performance of the production of welds. This automated welding process increases the speed, precision, quality and also minimises the chance of errors or inconsistent welds compared to manual welding.
Welding robots are very precise, move smoothly and at considerable speed through a programmed path. Being computer-based, they can be programmed and have sensors to follow the seam and to apply corrections to the welding parameters.
In arc welding and manufacturing in general, automation refers to some or all of the steps in an operation being performed in sequence by some mechanical or electronic means. Certain functions may be performed manually (partial automation); or all of the functions may be performed without adjustment by the operator (total automation). Automation can be applied to many different processes.
Equipment may accommodate a single assembly/family of assemblies (fixed automation), or may be flexible enough to be quickly modified to perform similar operations on different components and assemblies (flexible automation).
Some of the main machine types are:
- MIG/MAG welding
- TIG welding
- Joint finding and seam tracking Adaptive control
- Flexible manufacturing systems
- Process and robotic simulation
- Off-line programming
- Remote welding
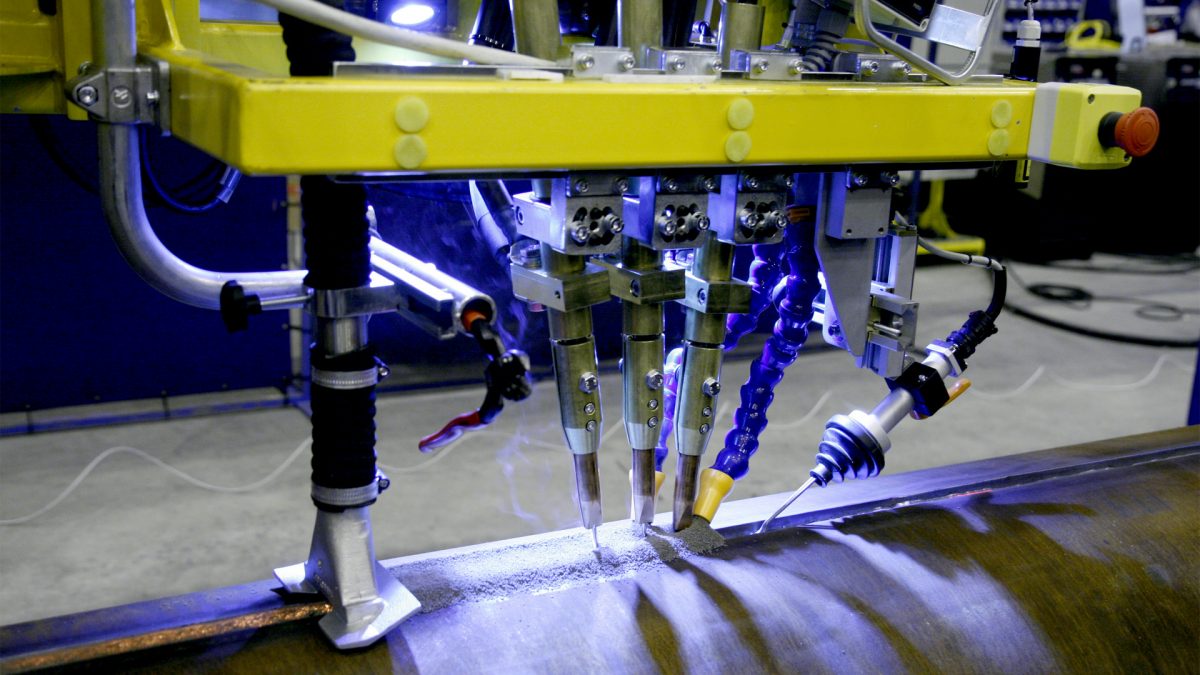
.jpg)